A hazard control program consists of all steps necessary to protect workers from exposure to a hazardous substance or other types of hazards such as noise, vibration and even cold temperatures and bad weather. It may well be a system, training or a set of procedures required to monitor worker exposure and their health. A written workplace hazard control program should outline which methods are being used to control the exposure and how these controls will be monitored for effectiveness.
How to define Hazard Control Types
Selecting an appropriate control is not always easy. It often involves doing a risk assessment to evaluate and prioritize the hazards and risks. In addition, both "normal" and any potential or unusual situations must be studied. Each program should be specially designed to suit the needs of the individual workplace. Hence, no two programs will be exactly alike.
Choosing a control method may involve:
- Evaluating and selecting temporary and permanent controls.
- Implementing temporary measures until permanent (engineering) controls can be put in place.
- Implementing permanent controls when reasonably practicable.
For example, in the case of a noise hazard, temporary measures might require workers to use hearing protection. Long term, permanent controls might use engineering methods to remove or isolate the noise source. Choosing exactly what type to apply depends on many factors normally boiling down to combination of intensity and frequency of workers exposure to hazard.
Main Ways to Control Hazards
hese methods are also known as the "hierarchy of control". Some sources may use a variation of this hierarchy. Regardless of the number of levels included, the hierarchy should be considered in the order presented.
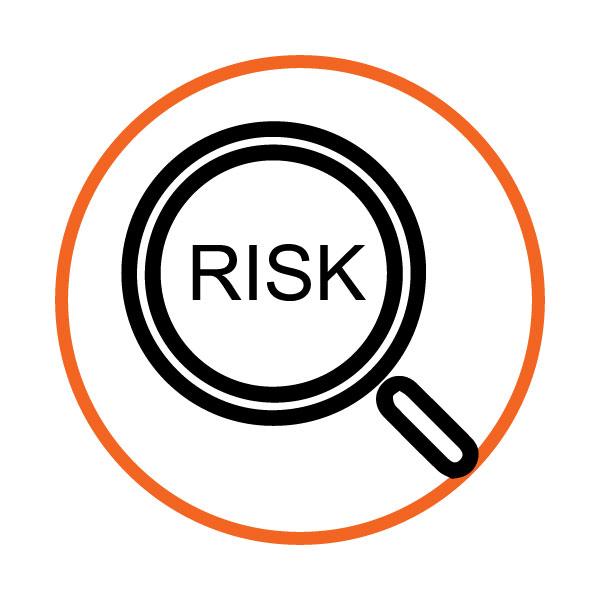
Elimination or Substitution
remove the hazard from the workplace, or substitute (replace) hazardous materials or machines with less hazardous ones.
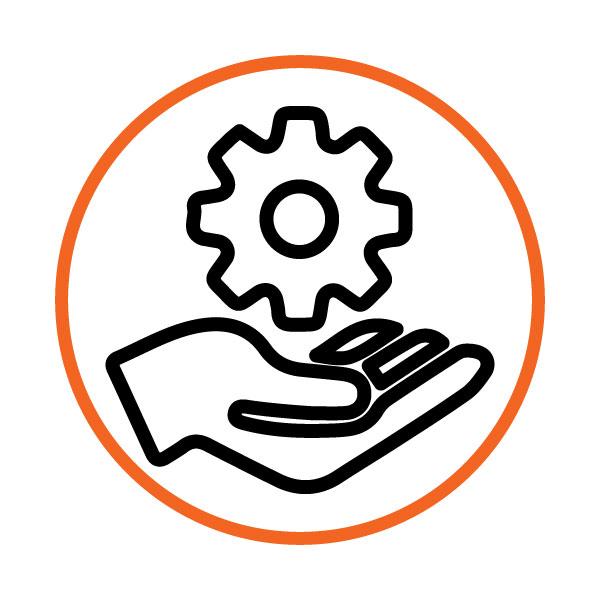
Engineering Control
includes designs or modifications to plants, equipment, ventilation systems, and processes that reduce the source of exposure.
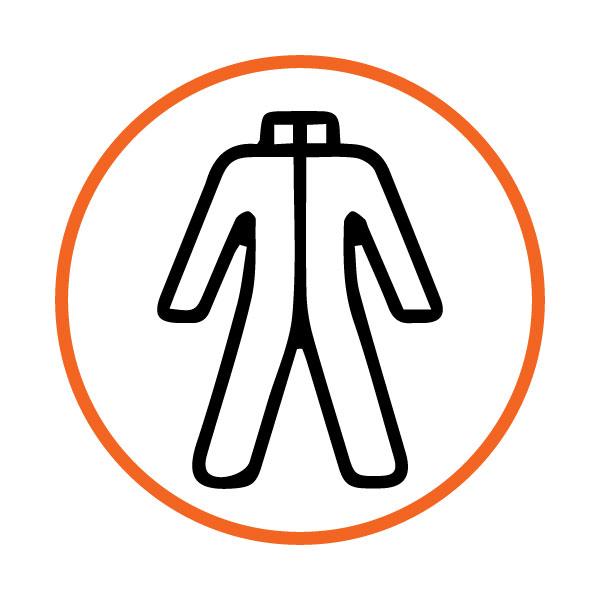
Engineering Control
includes designs or modifications to plants, equipment, ventilation systems, and processes that reduce the source of exposure.
PPE is the last control that is as important as others. This is where SGK becomes a valuable partner to industrial businesses to deliver ultimate safety comfort and personnel engagement with corporate workwear.
We design, test and manufacture a wide variety of garments using flexible materials. Our experience with garments design and material management is an asset to deliver an efficient PPE program to your business for variety of industries.
Personal Protective Equipment (PPE) as a Hazard Control Method
Personal protective equipment (PPE) includes items such as respirators, protective clothing such as work suits, coveralls, vests, gloves, face shields, eye protection, and footwear that serve as a barrier between the wearer and hazards (chemicals, dust, heat, frost, fire, water wind, and others).
It is the final item on the list for a very good reason. Personal protective equipment should never be the only method used to reduce exposure to hazards except under very specific circumstances because PPE may "fail" (stop protecting the worker) with little, or no warning and it is our job to make sure the chance of failure is minimal providing high quality for value.
Stay Updated!
Subscribe to our newsletter to receive more interesting content directly to your inbox.
Don’t miss out on the latest updates, insights, and exclusive offers!
Industrial Hazards Control