Welding operations are very common in metallurgy, ship building and repairs, construction, and other industries. Workplace environment for welding is generally harsh. The flame, arc, hot weldment, splashing molten metal droplets, red-hot electrode tip, and slag in the welding process are the main heat sources and hazards that cause welding burn accidents. Some materials must be preheated before welding. Heat, the preheating temperature may reach 150 - 300°C.
In addition to the hazards associated with high temperatures and heat, there is also a hazard to contact electricity during electrical welding. For example, one should consider wrong connection between live and neutral wires caused by the fault of electric welding equipment or line, reverse connection of the welding transformer and other many things that may go wrong, so electric shock is also one of the dangers of electric welding operations.
In summary, welding work remains one of the most hazardous operations at the workplaces. In addition to SGK's Welding and Extreme Fire collection containing garments specifically to protect welders' workplaces we provision shoes from our partners answering all requirements to keep workers safe during tough work. The minimum "must-list" describing the requirements:
Sole heat resistance
For low heat-resistant welding safety shoes, the heat-resistant temperature of the sole is required to be 150°C
For heat-resistant welding safety shoes, the sole heat-resistant temperature is required to be 250 °C
Electrical Insulation
The electrical insulation performance of welding safety shoe should withstand a voltage of 6kV, and the leakage current should not exceed 3mA.
Thermal Insulation
Welding safety shoes require good thermal insulation. The midsole of the shoe should be a material with good insulation.
Mechanical Protection
The physical and mechanical properties of the sole of the welding safety shoes and the peel strength of the finished shoe meet the requirements of the standard for molded leather shoes.
Stay Updated!
Subscribe to our newsletter to receive more interesting content directly to your inbox.
Don’t miss out on the latest updates, insights, and exclusive offers!
Uppers
The uppers of welding work shoes are generally made of bovine (positive, repaired, suede) leather, pig (positive, repaired, suede) leather or other natural leathers.
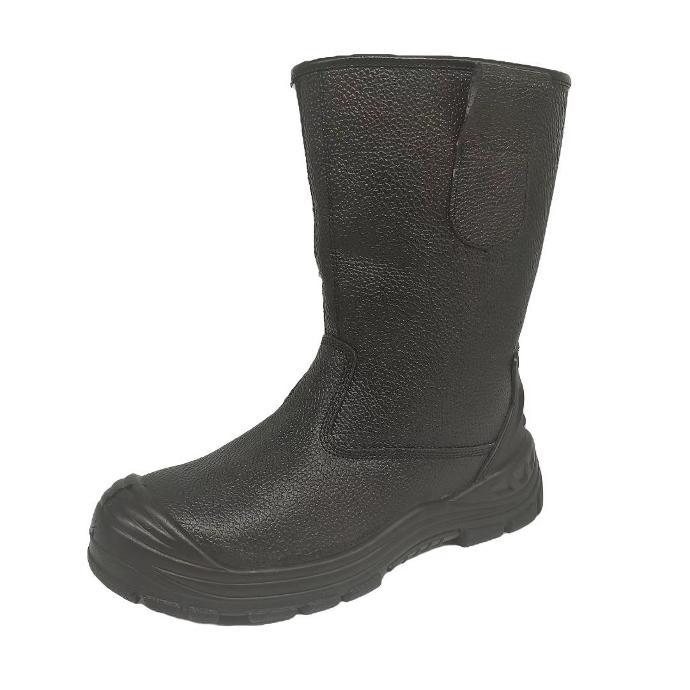
There are mainly positive leather, modified leather, suede, and other varieties of upper that can ensure these requirements are met. Pigskin, cowhide, and sheepskin are mostly used as raw materials, made of chrome tanned, generally dyed in various colors, and oiled with emulsion. Except for suede and individual unfinished leather (suede is unfinished), most of them are finished. Its thickness varies according to the requirements of different raw leather and shoemaking (between 0.5~1.8mm), and the thick upper leather without lining can reach more than 2.5mm.
The upper should have flame resistance, and the burning speed should not be greater than 1m/s. The combination of the upper and the bottom is formed by a molding process, the high waist style, and the foam soft leather roll opening at the top of the shoe, which is not only comfortable to wear but also protects the ankle from friction.
Cleab Safety Shoes
SGK features wide assortment of shoes suitable for welding in compliance with RoK regulations. Pick a model of your preference or contact us to develop a specific custom-made model for your business needs
Welding Safety Shoes